PSU-Behrend and Acutec integrate flexible collaborative robots into machining production lines
Nathan Snizaski
Oct 14, 2024
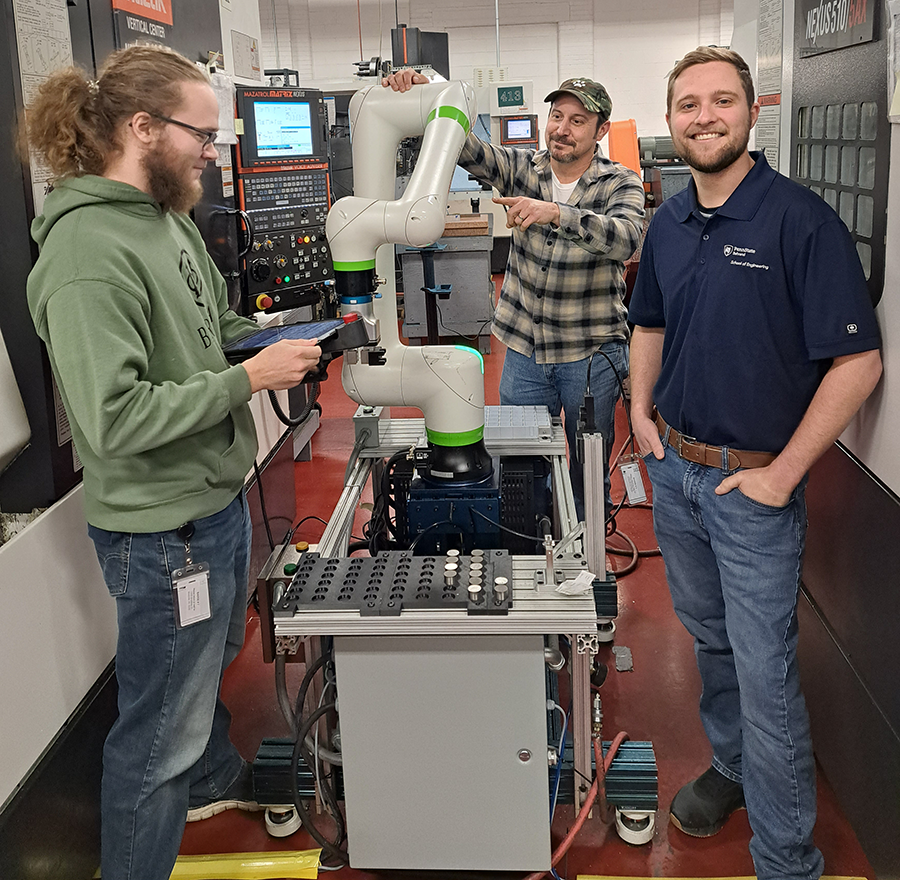
Fanuc cobot on a mobile cart interfacing with Mazak machine tool. Pictured: PSU-Behrend students Laurence Vorous (left) and Tyler Shearer (right) with Acutec Automation Manager and project mentor Adam Dunn (center).
Acutec Precision Aerospace (Meadville, PA) is a globally recognized precision machined metal component and subassembly supplier. Over the past 30 years, Acutec has become the largest industrial employer in Crawford County, with a workforce of over 400 Pennsylvanians. Recently, the company has been operating at less than 20% of its equipment capacity due to staffing and operational constraints, resulting in an increasing backlog of orders. To remain competitive, Acutec partnered with researchers at Penn State-Behrend to optimize equipment usage through automation.
In machining, integrating robots into production lines has been shown to boost productivity and provide an effective solution to a nationwide machinist shortage. Collaborative robots, known as “cobots,” are designed to work alongside humans in various industries, particularly manufacturing. Once programmed, cobots are ideally suited for the repetitive tasks common in machining operations.
Traditionally, cobot integration in manufacturing has been application-specific, with each cobot designed to work with a single machine and part combination. The challenge is creating flexible robotic systems capable of quickly adapting to the unique demands of different milling machines. With a flexible implementation, cobots can be easily re-purposed to operate across various machine and part combinations.
“We’re focusing on the flexibility of automation systems,” says Rubeo. “And by flexible, we mean that the robot can be rapidly repurposed to work for a different machine, a different process, using a different part.”
Rubeo’s research team developed a transportable cobot—a robot arm on a moving workstation—that can connect to various CNC machines at Acutec to communicate with their controllers, which execute the appropriate programs for producing specific parts. Once a human machinist connects the cobot to the CNC machine and equips it with the necessary tools, the cobot operates alongside the CNC machine without needing further human intervention.
“In the morning, after the cobot has been operating all night, workers would come in and replenish the material supply, and then the cobot would keep running,” says Rubeo. “As the project evolved, we introduced a material handling system to extend the need to replenish the material supply from every eight hours to every 24 hours, which enabled longer production times.”
What I learned through this partnership with Penn State-Behrend is that Acutec is also a learning facility. Pairing the brightest and best at Penn State-Behrend with the Acutec automation team was truly an eye-opener in regards to the brain power of these emerging leaders.
Adam Dunn, automation engineering manager, Acutec
Adam Dunn, an automation engineering manager at Acutec, praised the project’s success for “light out” manufacturing, where a fully automated production process operates without the need for human intervention, often during lightly staffed night shifts or during off-hours.
“At a time where labor is scarce, the system Acutec and Penn-State developed provides us with 100% unattended machining paired with true ‘lights out’ manufacturing,” says Dunn.
Acutec plans to further develop the unmanned cobot project internally, building on the achievements of Rubeo’s team by incorporating an inspection process. To help employees upskill, Acutec developed an automation engineering group, a team of engineers that work on solving automation issues that arise on a full-time basis and plans to cross-train machinists to support automation engineers.
Rubeo believes that the addition of the cobot plug-and-play technology will attract skilled workers to take on higher-paying jobs that require automation expertise.
“When you walk into a fully automated, state-of-the-art machine shop, it’s highly technical and very clean,” says Rubeo. “It's a very different picture of manufacturing from the early 1900s. For an engineer graduating from college or trade school, it’s an interesting time to be in manufacturing. Acctec is a huge company with probably the nicest machine shop I've ever seen in terms of general cleanliness and the quality of the machine tools. For machinists and engineers alike, facilities like Acutec are where you want to work because there's just so much advanced technology being used. That's kind of the impact I hope our work will contribute to Pennsylvania’s economy and Pennsylvania jobs.”
Dunn credits the Manufacturing PA program for supporting strategic partnerships between local companies and learning institutions to invest in Pennsylvania’s manufacturing industry. A
“I am amazed with the support and positive reinforcement of all the parties involved,” says Dunn. “Acutec partners with a lot of our local manufacturing facilities and industry partners, and the story of success resonates. This grant gave us the opportunity to invest in ourselves, help mitigate a skilled labor shortage, raise our profit with unattended machines running, and build a bond with one of our local universities. Penn State-Behrend supported Acutec by providing us with some of the brightest leaders emerging into the engineering field, so it is our obligation to pay that back with world-class training and opportunities to expand their work experience.”