HHG Drums and Penn State-Altoona develop innovative drum shell milling machine
Nathan Snizaski
Sep 5, 2024
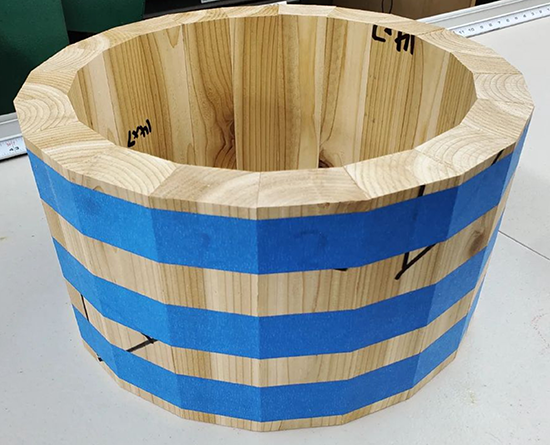
Drum shell made of glued wooden slates ready for machine milling.
Millions of Pennsylvanians enjoy playing musical instruments. While collectors and aficionados buy boutique instruments, students and hobbyists often purchase cheaper, mass-produced instruments to learn their craft. Custom drum manufacturer HHG Drums (Hollidaysburg, PA) partnered with researchers from Penn State-Altoona to reduce manufacturing costs, increase production yield, and appeal to a wider customer base through the implementation of a specialized drum shell milling machine.
HHG manufactures custom drums made from both locally sourced lumber and exotic woods, which drummers prefer for their superior tonal qualities and aesthetics over mass-produced products that use plywood. Due to a labor-intensive manufacturing method, the corresponding per-unit retail price of HHG’s instruments remains high. A major production bottleneck involves cutting large, polygonal wooden slats into a perfect cylinder to create the drum’s unique sound.
To create the drum’s “shell,” the main body of the drum, HHG glues vertical slats together in a ring shape, like a wine barrel. The interior and exterior sides of the wooden slats are then shaved into a cylinder using a rotary cutting tool — a process known as machine milling, where components are created by cutting away material from a fixed workpiece. HHG hopes to automate this time-intensive part of the manufacturing process to increase production and offer more affordable instruments to its customers.
The Penn State-Altoona team developed a programmable Computerized Numerical Control (CNC) milling machine that reduced unit production time by 25% with a superior cut accuracy of 95%, with a milling depth of more than 24 inches. Due to the limitations of its previous milling machinery, HHG primarily manufactured snare drums with shell depths averaging 5 to 8 inches. HHG now has the capability to cut multiple drums per session and explore new product lines, such as larger bass drums and acoustic drum sets.
“With the milling machine that we built, HHG can now stack four snare drum shells at a time on the machine, hit start, come back a few hours later, and all four drums will be cut,” says Craig Brennecke, professor of practice in engineering at Penn State-Altoona. “We not only made the machine robust and big enough to handle production of multiple drum shells at a time, but also automated the process so a worker could tend to other job responsibilities while operating.
Working with Penn State-Altoona on this project was a truly valuable experience for me and my company. As a team, we solved one of the core pain points for my business, and I gained a lot of insight from the research team about how to tackle a large and complicated manufacturing problem.
Sam Thurau, president, HHG Drums
Sam Thurau, HHG Drums president, believes the long-term benefits of the research partnership will result in accessing new markets domestically and abroad, which includes the majority segment of beginner and intermediate drummers.
“Currently, our company’s market share is a very small portion of the total addressable market for acoustic drum sales in the U.S. and abroad,” says Thurau. “If we are able to automate this key portion of the manufacturing process, it would create economic efficiencies that would allow us to enter into new markets abroad, as well as increase our domestic distribution network.”
Brennecke said that working with HHG Drums benefited students by working on a live project used in industry to prepare them for life after graduation.
“What I appreciate about this collaboration through the Manufacturing PA program is that my students get an opportunity to get a taste for what working in industry will be like before they graduate [from Penn State-Altoona],” says Brennecke. “Working with Sam and HHG Drums is the same thing as working in industry with the same expectations for working with a customer.”
Thurau believes that the local community benefits from partnerships such as the Penn State-Altoona collaboration by training and potentially retaining engineering talent for the future revitalization of the greater Altoona area.
“We believe in supporting the career development among local engineering students as a means of supporting our community, reversing the ‘brain drain’ and helping build the local economy.”