University of Pittsburgh and U. S. Steel investigate steel behavior in new processing concept
Nathan Snizaski
Oct 11, 2023
As auto manufacturers face demands to improve vehicle efficiencies, steelmakers are devoting resources to developing high-tech materials for the industry. Automakers desire high-strength, lightweight steels to improve vehicle performance while maintaining safety standards. United States Steel Corporation (U. S. Steel) collaborated with the University of Pittsburgh to characterize the microstructure development and precipitation behavior of advanced steel products for automotive applications.
Precipitates are extremely small particles intentionally formed in steels during solidification, thermomechanical processing (hot rolling), and during cooling after hot rolling to improve the overall strength and durability of the product. Engineers design alloy compositions to produce precipitates with determined size and distribution at critical processing points to create advanced steels with desired properties. U. S. Steel is developing a new production process for automotive applications where precipitates may occur at undesirable stages.
“This new process is much more efficient by directly coupling the casting operation to the rolling operation, where we can gain great benefits in energy efficiency,” says Matthew Merwin, senior research consultant at U. S. Steel. “This represents a remarkable change in the production process that may potentially produce fundamentally different behaviors in certain steel types.”
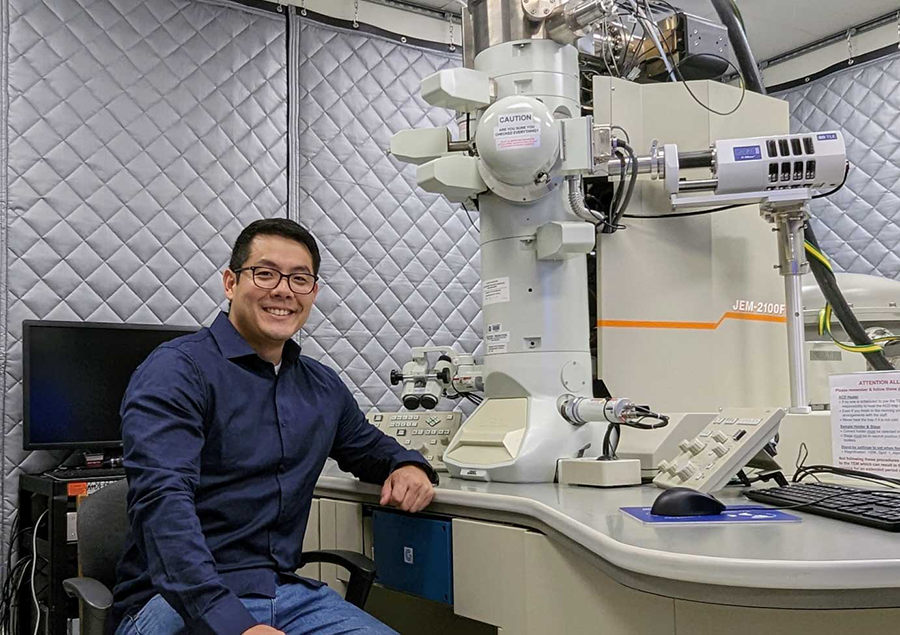
Source: University of Pittsburgh
University of Pittsburgh master's student Marcos Kendy Miyashima Moritugui
The steel products used in this project were engineered using experimental materials, requiring sophisticated equipment and skilled technicians to analyze these materials down to nearly atomic scale. U. S. Steel relied on University of Pittsburgh researchers' expertise, capabilities, and resources to do the detailed analytical work required to properly characterize these materials and establish a foundational understanding of steel behavior in the new processing concept.
“We want to understand this particular process for all types of steel that require precipitation strengthening,” says C. Issac Garcia, mechanical and materials science professor at the University of Pittsburgh. “These added elements are very expensive. If you are not doing the proper processing at high temperatures, you are going to be wasting the impact of the precipitates. And that translates into cost.”
Using lab-scale steel production equipment at U. S. Steel’s Pittsburgh facility, the research team melted and cast steel ingots at the laboratory using a unidirectional solidification mold. The team then interrupted processing at critical stages by breaking the mold to rapidly cool the steel and freeze its condition. Unlike most labs, the team can break the mold as soon as the alloy solidifies to characterize microstructure development and precipitation behavior at each stage.
The novelty of the mold design facilitates the ability to physically simulate the newer generation steel production facilities that directly link the casting operation to the rolling operation. This is a major deviation from a long-standing steel manufacturing process where a continuous casting operation would produce steel slabs to be inventoried for future use.
“With the new generation of steel production where we try to take advantage of the energy efficiencies available from directly linking the (casting and rolling) processes,” says Merwin, “we need to be able to separate the mold and extract the cast ingot while it’s still hot.”
We highly value our collaboration with the university and the opportunity to actively engage students to bring a new generation of potential engineers into the industry. Having access to the expertise of Prof. Garcia and his colleagues, along with the great analytical tools that the university offers, helps us gain further insights in areas that may not be achievable through internal efforts alone.
Matthew Merwin, Senior research consultant, U. S. Steel
Merwin says that physically simulating processing at the laboratory scale helped develop foundational knowledge through small-scale experiments rather than committing to an investigation on an industrial-size facility that could consume tens to hundreds of tons of material.
“We highly value our collaboration with the university and the opportunity to actively engage students to bring a new generation of potential engineers into the industry,” says Merwin. “Having access to the expertise of Professor Garcia and his colleagues, along with the great analytical tools that the university offers, helps us gain further insights in areas that may not be achievable through internal efforts alone.”
“We’re in the business of education, the business of developing knowledge,” says Garcia. “Every time we get a project like this, it’s exciting to be able to go to a larger-scale setting—not just work under laboratory conditions at the university—and put these ideas into place. Projects like these are a tremendous opportunity for students to see that the industry needs this type of education and research.”