Reducing prosthesis fitting time through additive manufacturing
Jacob Williamson-Rea
Aug 16, 2022
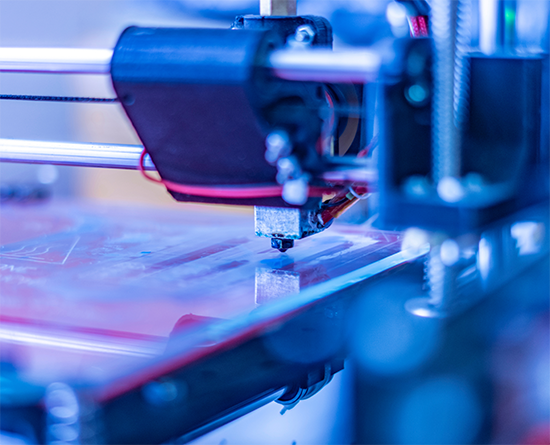
Although awareness of prostheses has grown in recent years through mass media, the area of prosthetics manufacturing remains a very small industry compared to other medical fields. The field of prosthetics has been in existence for centuries but is now exploring the modernization of patient care through additive manufacturing.
Most prosthetic manufacturing companies utilize traditional methods of hand casting to customize external limb prostheses–a labor-intensive process that requires plaster molding, shaping, and buffering by hand. Through additive manufacturing–the process of creating an object by building it layer by layer–the time to create a patient-specific prosthesis is significantly reduced, thereby speeding up patient care. Robert Morris University and Union Orthotics & Prosthetics Co. joined forces to investigate the feasibility, strength, and integrity of 3D printed prosthetic sockets.
Won Joo, associate professor of biomedical engineering at Robert Morris University, explains that the focus of the project is to minimize the total time needed to print a patient-specific prosthesis without compromises. “How can we minimize the printing time by controlling printing conditions, shape, and many other factors while maintaining the integrity of the socket comparable to traditional hand casting? That’s the question we’re investigating,” says Joo. As of this writing, his team has optimized printing conditions to achieve a 3D print of a prosthesis within 10 hours, down from 30 hours. With additive manufacturing technology constantly improving upon itself, the collaborators now ponder: Can we print a prosthesis within a reasonable timeframe while a patient is waiting in the lobby of a medical specialist?
“That’s the ultimate goal,” says Peter Leimkuehler, Clinical Director of Prosthetics & Adult Orthotics at Union Orthotics & Prosthetics Co., based in Pittsburgh, PA. “The printers are maybe 3.5 feet wide, 3.5 feet long, and about 4 feet tall, so it’s a smaller machine. So, ideally, a patient would come to our office, we would scan their limb, modify the scan on the computer, print it, and fit the patient before they leave–all within the same appointment.” By comparison, the traditional hand casting method requires a lengthy process of creating a plaster cast of the patient’s limb and making very fine adjustments by hand to ensure both socket integrity and patient comfort. “With 3D printing, we would skip over several steps done by hand and go right to the final product that the patient’s limb would go into.”
The potential benefits of additive manufacturing used to print patient-specific medical devices include better outcomes and quicker turnaround for patients. “When we fabricate things by hand, it’s always very labor-intensive and not always reproduceable,” says Leimkuehler. Occasionally, specialists have trouble reproducing a patient’s socket by hand with the exact specifications used with the first prosthesis, or with the slight changes needed when a patient’s limb changes. “With additive manufacturing, we have the files. We can reprint it–make tweaks to it as needed,” Leimkuehler explains. “We’re always striving to get patients up and on their feet again, and it’s a very rewarding feeling to help them do that. To be able to speed up that entire process would help us help our patients to an even greater degree.”
Through this project, Joo and co-PIs Arif Sirinterlikci and Rika Carlsen believe they are building the fundamental knowledge to optimize 3D printing to that of out-patient care with minimal wait time. “From an engineering perspective, our team is trying to understand what kind of printing technology is best for this type of product,” says Joo. “Once we know more about what printing conditions make for a really good 3D-printed socket, we’ll be able to meet our goal of a quick print time that’s reasonable for a patient to wait in a lobby to be fitted that day–and that time will probably come sooner than later.”To be able to speed up the entire process would help us help our patients to an even greater degree.
Peter Leimkuehler, Clinical Director of Prosthetics & Adult Orthotics, Union Orthotics & Prosthetics Co.