Climate control for additive manufacturing
Nathan Snizaski
Jul 8, 2022
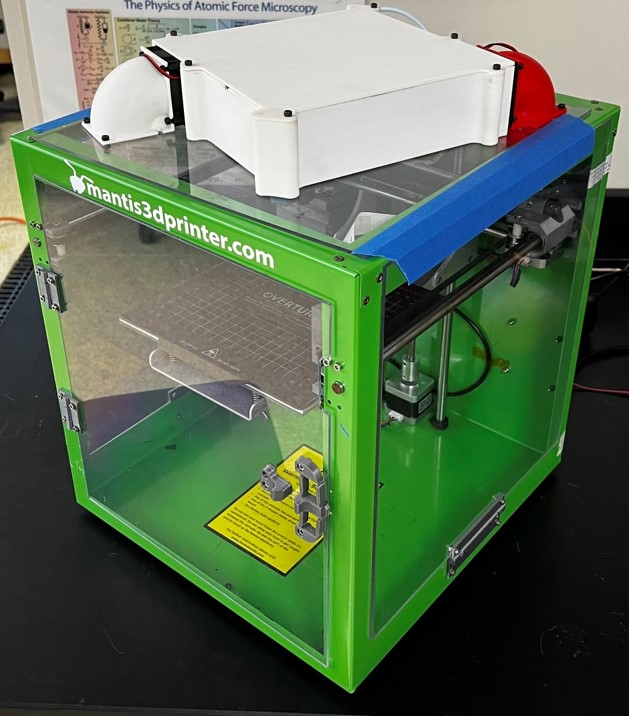
In additive manufacturing, also known as 3D printing, materials are deposited layer by layer from a printer to create a 3D object. Compared to traditional manufacturing processes, the immediate benefits of 3D printing include less material waste, reduced manufacturing time, and more complex design shapes through advanced controls. However, polymers used to print the layers of material are very sensitive to environmental conditions–such as temperature and humidity–especially when the polymer is at its melting point. These different responses to high and low levels of humidity impact the strength and integrity of printed parts. Manufacturers seeking high tensile strength and durability while printing specialized devices in high humidity environments would not achieve the same results as low humidity environments. Widener University and Verde Mantis came together to take on the challenge of ensuring consistency in desired 3D printing output through climate control.
“What we are doing with this project is designing and fabricating an enclosure around 3D printers where we can control humidity–low or high, depending on the application we are dealing with–throughout the whole print volume,” says Babak Eslami, assistant professor of engineering at Widener University. “In simpler terms, it’s just like how you turn on your AC and heater in your bedroom to feel comfortable–we’ve designed an AC and heating system for our 3D printers to print in a comfortable environment.” Kamran Fouladi, associate professor of mechanical engineering at Widener and co-PI, expands on this point by stating that the Widener enclosure design can be used to print very specific applications depending on the level of humidity needed for the device or the object you wish to print.
Manufacturers may seek to print material under specified conditions to optimize the desired effect of the device or object. Printed under low humidity conditions, a prototype can support high levels of durability and structural integrity when being pulled or pushed on during its application, like a load bearing device. On the other extreme, high humidity printing conditions will increase the likelihood of 3D printed materials intentionally breaking at certain stress levels. For example, consider mechanical switches or actuation mechanisms.
“Let’s say you have a linkage that you want to break at a certain point to actuate another mechanism that will follow, perhaps in an assembly line or in a mechanical design,” says Eslami. “With our design, you basically have a control knob on a 3D printer that relates to the desired strength of material, whereas you do not have that feature through a traditional manufacturing process.”
Even as 3D printing is becoming more prevalent in manufacturing processes, companies may yet be challenged to produce specific 3D printed applications due to the humidity level in their facilities.
“Think of a manufacturing plant or warehouse with many 3D printers working,” says Fouladi. “The printers may be doing different applications and the warehouse can be very humid or very dry, depending on the ambient environmental applications. For the best outcomes, you can actually control specifications for different applications for each printer with our enclosure design. Or you could even set all printers to print material under low humidity specifications within the enclosure, even though the warehouse has high levels of humidity.”
“It’s exciting to see the aspects in how smaller-scale 3D printers can be optimized to produce more consistent results,” says Widener undergraduate student and researcher Andrew O’Donohue. “Desktop printing at this point is more of an art than a science, for the most part, because you’re turning knobs to see what works and what doesn’t through the output. Doing this type of research gives us the ability to start tuning signal parameters and studying how the technology can be optimized to produce more consistent parts without trial-and-error and spending hundreds of thousands of dollars on expensive additive manufacturing equipment.”
The Widener team looks toward the bright future of additive manufacturing. “3D printing changed the game,” says Eslami. “Engineers can think of an idea for a few hours, and for a few dollars of printing material, you can have the part in your hands that day to further improve that design. The time that you would spend as an engineer to design a fully functional part is truly minimized by the capabilities of 3D printing.” Eslami believes that any field that goes through the product development process can benefit from 3D printing and further enhance the desired strength of printed material through the Widener enclosure design.