University of Pittsburgh and Carpenter Technology Corp. refine magnetic alloy processes
Jacob Williamson-Rea
Jun 1, 2022
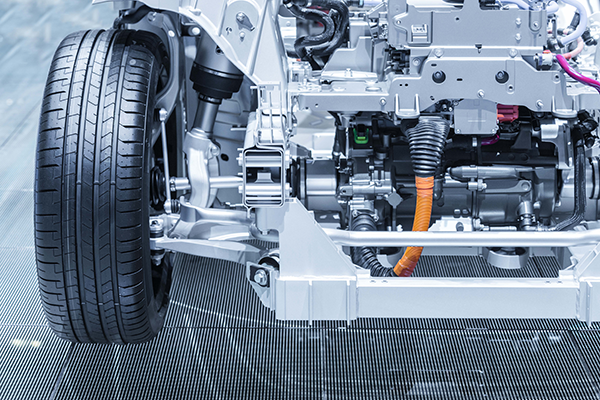
This industry/academic team of the University of Pittsburgh and Carpenter Technology Corp. partnered up to refine new manufacturing methods for existing magnetic alloys.
"Magnetic alloys are used in a number of applications currently, and they're becoming very important, even more so than they have been historically," says Paul Ohodnicki, associate professor of mechanical and material science at University of Pittsburgh. "There is a class of alloys called soft magnetic alloys that magnetize and demagnetize with relatively low energy losses.” This special class of alloys is used in transformers in energy grids, as well as in electric motors, such as those in electric vehicles (EVs). “Soft magnetic alloys are a critical link when converting electricity between different forms, such as converting different voltages and currents in a transformer or converting electrical energy to mechanical energy like in an electric motor in EVs."
Ohodnicki says that materials like soft magnetic alloys are becoming increasingly important due to the huge electrification trend. Vehicles are becoming electric, there are more renewables on the grid, and overall, electricity is becoming a larger portion of our total energy utilization. "For this project, Carpenter Technology and our team wanted to explore and improve existing alloys that are in the market today,” says Ohodnicki. “The PA Manufacturing opportunity made the linkage with Carpenter Technology possible, and to have the financial resources needed to spend some time working on it, which is not trivial.”
The PA Manufacturing opportunity made the linkage with Carpenter Technology possible.
Paul Ohodnicki, Associate Professor, University of Pittsburgh
Carpenter Technology Corporation, based in Philadelphia, PA, has a whole class of soft magnetic alloys, and when a motor is constructed, the importance of both the magnetic and mechanical properties is very high, because there are rotating parts, parts that must withstand rotation, mechanical torques, vibrations, and more. This means that there is always a trade-off between the ability to make something as energy efficient as possible from the magnetic and electrical standpoint, but the parts must also be as mechanically robust as possible. Traditionally, when alloys are annealed, a process that tailors the magnetic and mechanical properties, engineers have had to make significant trade-offs between the two properties.
"By using advanced manufacturing, we can actually tailor both magnetic and mechanical properties on a single lamination of the material. Rather than using discrete annealing conditions, we can locally anneal the material in specific regions,” Ohodnicki explains. “This breaks the trade-off cycle and allows us to vary the properties, and allows us to better understand the actual needs of the alloy in the device or application in which it will be used, such as a motor."
Ohodnicki noted that the Manufacturing PA Innovation Program enabled him to welcome Tyler Paplham, a University of Pittsburgh Ph.D. candidate, to his group. Ohodnicki says that the grant provided significant financial resources necessary to support Paplham’s doctoral studies, with the Carpenter Technology collaboration assigned as Tyler’s first research project.