New applications for ultra-lightweight foamed glass product line
Nathan Snizaski
May 25, 2022
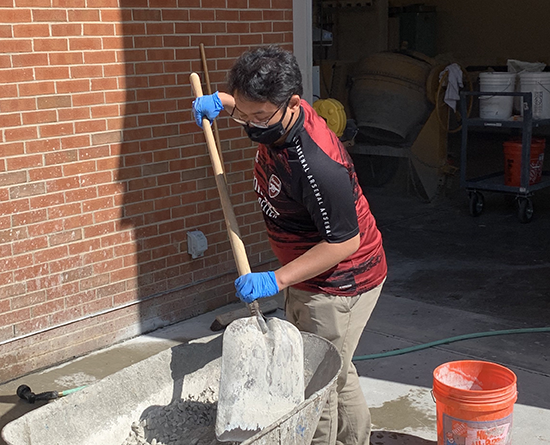
The production of solid waste is growing at a substantial rate in the United States due to increased consumerism and single-use products with disposable packaging. Without an existing recycling infrastructure, solid waste, such as paper, metals, and glass, is disposed of in landfills. Repurposing solid waste in manufacturing processes can mitigate some of the effects of a “throw away” culture by giving single-use products a second life. Aero Aggregates of North America LLC, based in Eddystone, PA, manufactures an ultra-lightweight foamed glass aggregate product made from 100% recycled container glass, diverting millions of bottles from landfills annually. To explore the expansion of its product portfolio, Aero Aggregates partnered with Penn State-Harrisburg to investigate different applications of foamed glass aggregate in precast concrete products.
Aggregates are granular raw materials, such as gravel and limestone, that serve as a vital ingredient to strengthen concrete. Unlike traditional aggregates produced from natural resources like shale and clay, Aero Aggregates produces foamed glass aggregates from 100% recycled glass–a thermally efficient product that is up to 85% lighter than quarried aggregate. While foamed glass aggregate as a product is not patented, Aero Aggregates does have some patented and patent-pending applications for foamed glass aggregates, including the use of foamed glass aggregate in composite materials such as concrete.
“We were intentional in focusing the project on precast concrete applications because we see so many advantages,” says Theresa Loux, Chief Technical Officer at Aero Aggregates. “With foamed glass aggregates, you significantly reduce the total weight of concrete products. You can then ship the material farther or load more units per shipment because of its lighter weight.” The lighter weight should also make it safer on job sites because the concrete will be easier to move and place.
An additional benefit to adding foamed glass aggregate to concrete casting over traditional aggregate material is its thermal efficiency, preventing unwanted temperature fluctuations in commercial buildings. While Aero Aggregates has had success using foamed glass in sub-slab applications, expanding its use in concrete casting for building enclosures presents an opportunity to support the design of sustainable, comfortable structures.
“Foamed glass is thermally efficient because of its incredibly lightweight structure–it’s a good insulator,” says Grady Mathews, assistant professor of civil engineering in the School of Science, Engineering, and Technology at Penn State-Harrisburg. “There are many benefits to adding it to concrete structures. It will make concrete lighter and retain heat better.”
Using foamed glass aggregates in construction applications serves as a viable alternative to mining finite resources while simultaneously addressing Pennsylvania’s growing solid waste problem. “This project also introduces an aspect of sustainability because we’re using a waste product in a secondary product life instead of just disposing of it in Pennsylvania landfills.”
Since commencing the project with Mathews’ team, Aero Aggregates has taken steps to expand its product offerings and scaling production. “This project has granted us access to the expertise of Grady and Penn State, as well as the research support from Grady’s students,” says Loux. “Working with their team helped us connect the dots on problems that Aero Aggregates is trying to solve. It’s been great to have resources from Penn State to help us work towards answering these outstanding questions that we have that will enable us to expand our markets.”
The success of the partnership between Mathews and Aero Aggregates has led to another PA Manufacturing grant funded for 2022. “We’re comfortable working with each other and I think we’re both getting a lot out of the collaboration,” says Loux. “Hopefully this new project that we’re working on isn’t the end. We’ll keep coming up with new ideas to explore different application areas. It’s been great.”We’re comfortable working with each other and I think we’re both getting a lot out of the collaboration.
Theresa Loux, Chief Technical Officer, Aero Aggregates